How To Reduce Operating Costs of Warehouse Operations Through Digital Twin Simulation
- Chris Brett
- Jun 17, 2024
- 5 min read
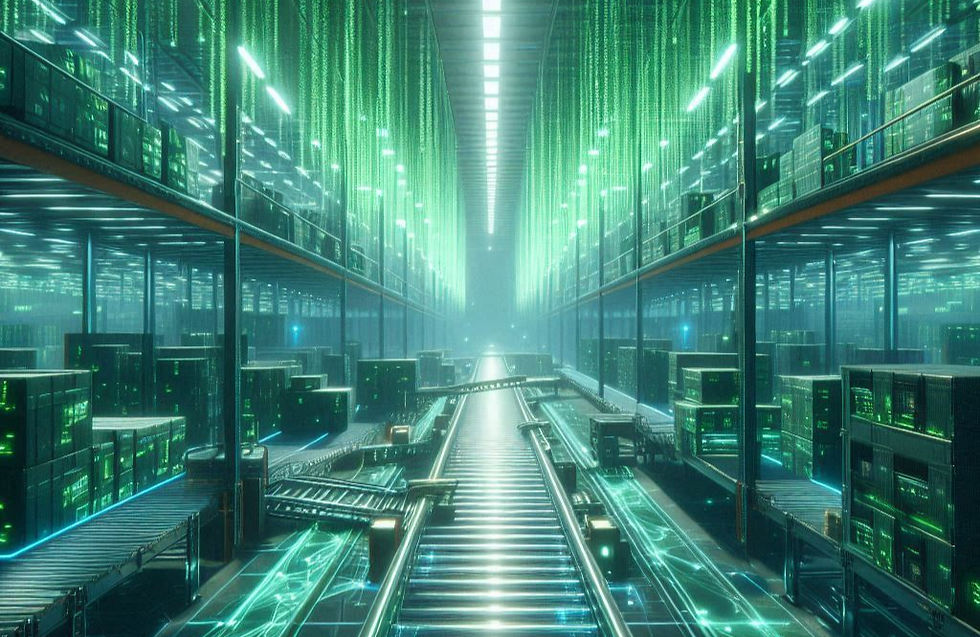
The running costs of fulfilment and distribution centres are significant. Optimising these costs down greatly affects profitability. As such, this is a key focus of teams that oversee the technology and operation. However, knowing what to change to reduce costs can be highly complex.
There are many factors that contribute to operating costs. Some are relatively hard to affect, e.g. warehouse rent, insurance, cost of goods. Some are better candidates for optimisation, such as:
Labour
Maintenance
Electricity
Waste
Labour
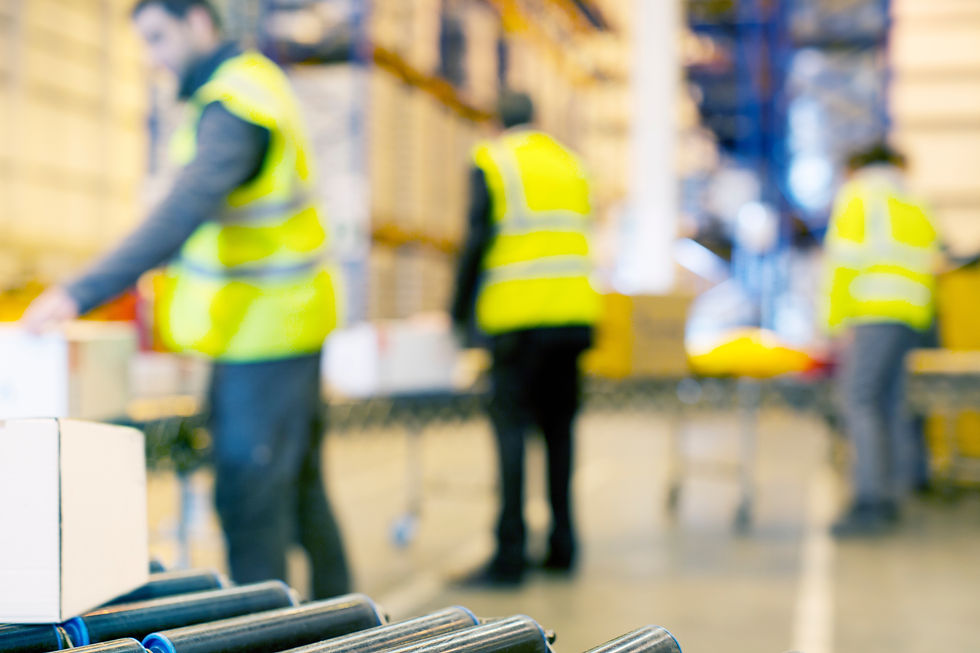
Even in highly automated facilities, labour costs are still generally one of the largest costs. Picking and packing is still generally done manually, though robotics is becoming more and more capable. Site productivity is often measured in terms of how many units of goods can be processed and dispatched per hour, per person. This can range from 50 to 1000, so there is often a lot of room for improvement.
Increasing the productivity of your workforce means you won’t need as many staff to get the same amount of work done. There are lots of different ways that this could be achieved.
The most obvious is to automate more of your manual processes, though this can require a large investment.
Another approach is to alter your processes to reduce inefficient use of time. You could analyse your manual processes to find times when your staff are not doing anything, and look for ways to keep them busy more of the time. This could involve things like adding buffer locations such that they are less likely to run out of work.
However, even if your staff are busy 100% of the time, they aren’t necessarily efficient. There could be things about their process that could be sped up, for example by adding something like a pick to light system so that they spend less time looking for what they need. Or they could be spending a lot of their time busy doing tasks that are secondary to their main goal of picking, e.g. walking to and from storage locations, or to different work stations. These sorts of things can often be optimised through systematic changes, such as optimising where goods are stored in order to reduce walk times - no hardware change required.
Even if your staff are working 100% of the time, and have an efficient work process, they may not be motivated to work quickly. Monetary incentivisation linked to their speed can help here. You need to be careful that this doesn’t increase inefficiencies in other areas though, such as waste caused by damage due to rushing.
Maintenance and Electricity
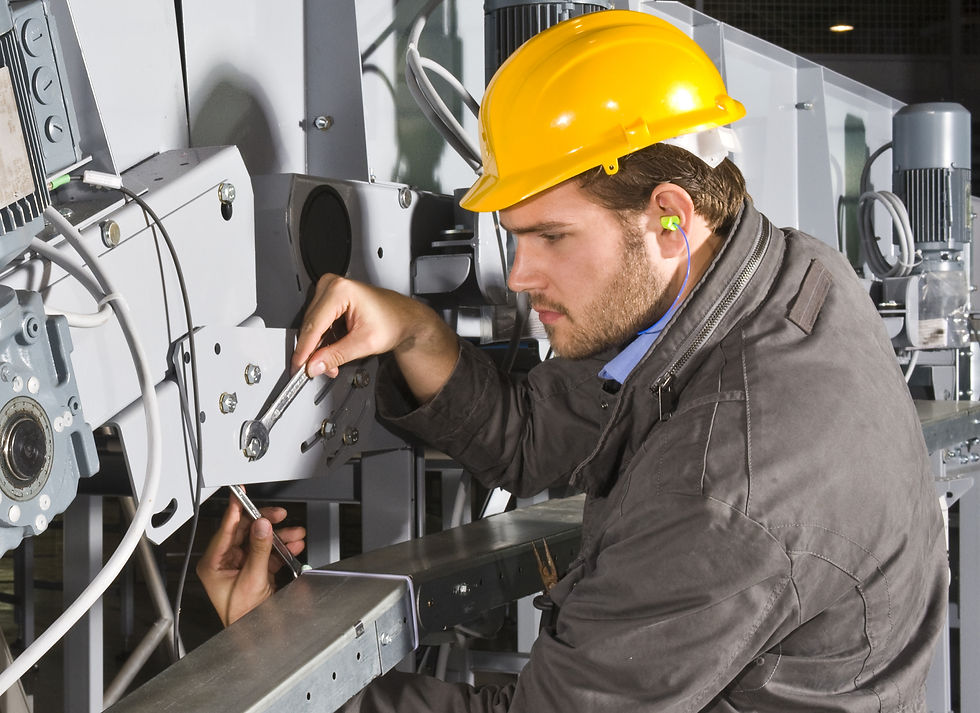
These are more significant factors the more automated your facility is. That automation needs power, and moving parts wear and break. There are things you can do to reduce these costs though, without reducing your usage of automation (which would drive up labour cost).
Some common techniques are usually built into systems you buy from third parties, such as conveyor belts automatically stopping when not in use. This saves power, as well as reducing wear, which reduces the amount of maintenance required.

A more complex approach is to minimise the amount of movements needed to process and dispatch an item. For example, this could take the form of optimising your conveyor routing system such that your goods take more direct routes from A to B. Or it could take the form of optimising where you store goods, so that there is less conveyor between an item and where it is needed. This approach reduces how much your automation is used for a given throughput, which reduces power usage and wear. Another effect of these types of optimisations is that you can generally handle a higher throughput with the same hardware.
Waste

In most operations, goods are sometimes written off. This could be due to:
Breaking the item (e.g. a picker drops it on the floor)
Losing the item (e.g. it isn’t tracked correctly, and the system doesn’t know where it is)
Expiration (e.g. items passing their sell-by dates)
Automation can sometimes help reduce breakage. If a process is repetitive, a machine can generally do it more consistently than a person.
Better systemic tracking of goods can help prevent losing the item - things like barcode / RFID scans whenever an item is moved.
Optimisations around how much stock to order, and which stock to use to fulfil orders can help reduce waste due to expiry. These optimisations will have to balance waste against things like out-of-stock levels and throughput.
With so many things that can be optimised, how do you choose which to target?
We say this a lot. This is the core choice that we need our clients to understand. There are two common approaches:
Making educated guesses, followed by trial and error in the real world, or
Building a simulated model or digital twin of your operation and using it to quantify what each change would give you
The latter is cheaper, faster, less risky, and results in a more optimal operation. Here’s how simulation can be applied:
You create a digital twin simulation. You use this to explore each candidate for cost optimisation. You model the change, run the simulation, and see how much it affects your operating costs. This allows you to quantify the benefit before implementing it in the real world. It also avoids you pursuing optimisations that either don’t work, or don’t have a good return on investment. It allows you to focus on the optimisations that give you the best bang for buck.

It’s important to have confidence you’re making the right decision, and therefore you need to ensure that the simulation is accurate. You do this by comparing the simulation’s predictions with what actually happened in the real facility on a selection of days. If the predictions are very close to what really happened, then the model is accurate. If they aren’t close, more work must be done to increase the accuracy of the simulation before using it for predictive purposes. This generally involves modelling aspects of the simulation in a higher fidelity. For example, if you were only modelling constant speed movement of a vehicle, you may need to model acceleration to make it accurate enough.
Data driven decision making can reduce the fear and uncertainty which comes with needing to reduce costs in production and distribution centres.
Our engineers have created simulations used to design and optimise the most advanced fulfilment centres for many of the world's leading online grocers. With over a decade of experience working with operations, warehousing and logistics, we have a proven track record of helping organisations like yours achieve significant improvements in operational efficiency and cost savings.
If you would like to talk to us about how we can help optimise your operation through simulation and digital twins, get in touch.
Comments